About the Customer:
This is a part of Embitel solution offerings perfectly suited for potential tier-1 customers looking for a customizable e-cycles or e-bikes.
Business Challenges:
In our pursuit of crafting an innovative electric cycle, we aim to blend engineering excellence with a keen understanding of customer requirements.
Leveraging Embitel’s 17+ years of industry experience, we approached the development stages with careful consideration. However, navigating the intricacies of this dynamic landscape reveals several challenges-
- Integration Challenges: Achieving a compact and integrated propulsion solution can pose integration challenges. Ensuring that all components work seamlessly together may require significant engineering efforts and testing.
- Verification and Validation Complexity: The emphasis on ease of verification and validation throughout the development stages can be challenging. Rigorous testing and validation processes are essential, but they can be time-consuming and resource intensive.
- Adaptation to Different Environments: Creating a system that works seamlessly across various environments may be challenging. Factors such as different terrains, weather conditions, and user behaviors could impact the electric cycle’s performance and reliability.
- Compatibility with Existing Systems: Aligning the development approach with the customer’s existing system may require adapting to diverse technological ecosystems. Ensuring compatibility and integration with existing infrastructure can be a complex task.
- User Experience Optimization: Balancing the engineering requirements with an optimal user experience poses a challenge. The design must not only be technically sound but also user-friendly and intuitive for a broad range of users.
- Cost Management: Developing an efficient electric cycle while managing costs is a constant challenge. Balancing performance, features, and affordability requires careful consideration throughout the development process.
Embitel’s Solution:
Since our team was tasked with developing the BLDC Hub Motor Control Platform for E-bicycle Application, we first performed a thorough study of the BLDC hub motor characteristics. We assessed the different components of the application software and identified the following approach for the development of the required motor control platform for our e-cycle project.
Our solution provides a BLDC Hub Motor Control Platform Solution range from (250W-3kW) for E-Cycle Application with the following Control strategy and integrated features.
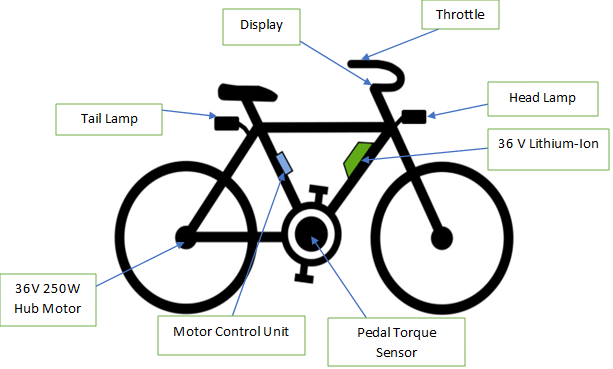
Control Algorithm for E-bicycle application –
Field Oriented Control (FOC)
Features Included in the Display –
- Battery SOC Indicator
- Odotmeter/ trip meter
- Speed
- Pedal Assist Modes
- Manual and Auto Mode
Model Based Development (MBD) –
- Development of BLDC motor control algorithm and features in MATLAB/Simulink
- Model in the loop simulation testing
- Code generation and integration
- Software in the loop testing
- Integration and testing
The scope of the project includes Motor Control application for Electric Cycles, with the following features of BLDC Hub Motor –
- Brushless Operation: BLDC hub motors don’t use brushes to function, as the name implies. By doing away with the requirement for physical interactions, this design lowers wear and friction while increasing overall efficiency. It also lasts longer and requires less maintenance when there are no brushes.
- Integrated Design: BLDC hub motors have a compact and streamlined design since they are frequently built into the wheel or wheel hub. By this integration, the exterior transmission systems’ complexity is decreased, and the vehicle’s overall structure is made simpler.
- High Efficiency: The remarkable efficiency with which BLDC hub motors transform electrical energy into mechanical energy is well recognized. By precisely controlling the motor, the electronic commutation system maximizes power supply and reduces energy losses.
- Quiet Operation: BLDC hub motors operate quietly in part because of the electronic commutation mechanism and the lack of brushes. This functionality is especially helpful for devices like electric bicycles, bikes, and scooters where noise reduction is a top priority.
- Precise Speed Control: Accurate speed control is made possible using BLDC hub motors, enabling seamless acceleration and deceleration. For applications where precise speed regulation is required, such as electric vehicles and robotics, this functionality is vital.
- Compact and Lightweight: Because of their generally lightweight and compact form, BLDC hub motors are appropriate for situations where weight and space are crucial considerations. For electric bicycles, bikes, and scooters, where weight reduction is crucial for efficiency and maneuverability, this feature is of utmost priority.
- Low Maintenance: BLDC hub motors require less maintenance than brushed motors because of their brushless nature. These motors have longer lifespans and require less regular repair because there are no brushes to wear out.
- High Torque to Weight Ratio: With a high torque-to-weight ratio, BLDC hub motors can deliver a lot of power in a comparatively tiny and light package. Applications where efficiency and acceleration are critical will benefit from this feature.
Embitel Impacts:
The BLDC Hub Motor Control Platform made the existing system easily configurable and maintainable to support future changes.
This challenging, motor control development project was completed within the desired time-lines and costs. This ensured reduce time-to-market and development costs for our client.
An EV friendly BLDC Hub Motor Control Platform has become a necessary requirement present day EVs 2 wheelers. Hence, the success of this project surely makes us dream big, of a long-term positive impact on the various business engagements of our customers.
Tools and Techniques:
Software
- MATLAB
- MBD
- Model in loop simulation,
- Software in loop simulation
Base software
- Handwritten c code by automotive team
Hardware
- DSpic microchip controller
- TI controller