Automotive Body Control Module – Ready To Deploy And ISO 26262 Compliant
In our journey of 16+ years, we have built a team of experts in automotive electronics, problem-solvers and designers (Embedded Hardware & Software).
We are also part of the trusted ecosystem of Automotive partners. This enables us to deliver Body Control Module solutions and Automotive ECU development services.
Features of Our Body Control Module ECU Solution
Our Embedded Software and Hardware development team has delivered automotive electronics solutions ranging from HVAC Control System, Seating Control, Adaptive Lighting Control, Power Windows, Smart Actuators and more.
The following are some of the important value-adds, that have ensured success of our Global Production Programs (in US, UK, China, South Korea, Taiwan and India)
- Reduce time-to-market with our automotive grade reference body control module ECU designs. Our automotive developers can quickly customize these BCM ECU solutions as per your business requirements (compliance with AUTOSAR and ISO 26262 Standards (ASIL B/ ASIL C/ ASIL D).
- This includes reference hardware design, CISPR, ISO/IECBoard Support Package(BSP), in-vehicle networking and vehicle diagnostic stacks (UDS (ISO 14229), OBD2) and motor control applications (ASIL B/ ASIL C/ ASIL D Compliant).
- Leverage our years of R&D efforts and domain expertise in motor control solutions for both BLDC motors and PMSM motors.
- Our Motor Control Solution is equipped with FOC algorithm for smoother and efficient operation of Brushless DC (BLDC) and PMSM motors.
- With our reusable and ready-to-deploy in-vehicle networking and vehicle diagnostics software, your team gets the freedom to focus on core product development tasks.
- FOC algorithmBusiness Model: One-time licensing fee model. In this business model, you (as the customer) own the IP rights and the source code of the software stack.
- This enables you to integrate the Automotive Software Solutions (UDS Protocol Stack, OBD2 Protocol Stack, J1939 Protocol Stack & more) across multiple projects and/or product lines.
- Automotive Stack Services: Integration, configuration and customization of in-vehicle networking and vehicle diagnostics stacks – UDS (ISO 14229), J1939, KWP2000, ISOBUS (ISO 11783), OBD2 (ISO 15031), CAN FD and more
- BCM has been developed using model based development approach with the help of MATLAB/Simulink tools.
- The Body Control Unit is AUTOSAR Compliant, taking it a step ahead in standardization demanded by the Automotive Industry.
- Our Body Control Module reference design has been developed as per ISO 26262 standard guidelines.
- We provide support for ASIL B, ASIL C and ASIL D compliance.
A Snapshot of Our BCM Platform’s Features
Our ISO 26262 compliant BCM platform offers a host of built-in features – each one of them designed, developed and tested using the most advanced tools.
Following are the built-in features of our BCM platform
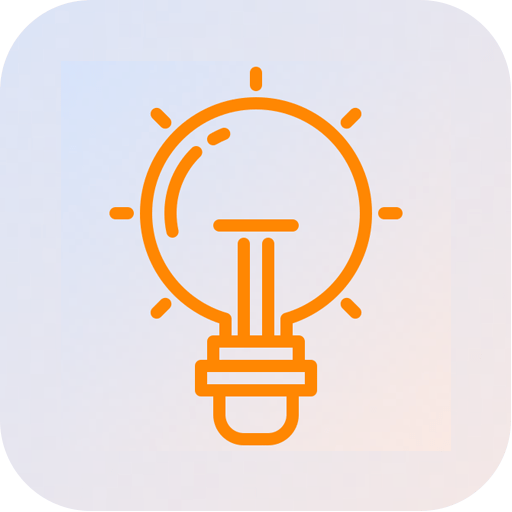
External and
Interior lighting
- Head lamp
- Indicators
- Tail lamps
- Cabin lamps
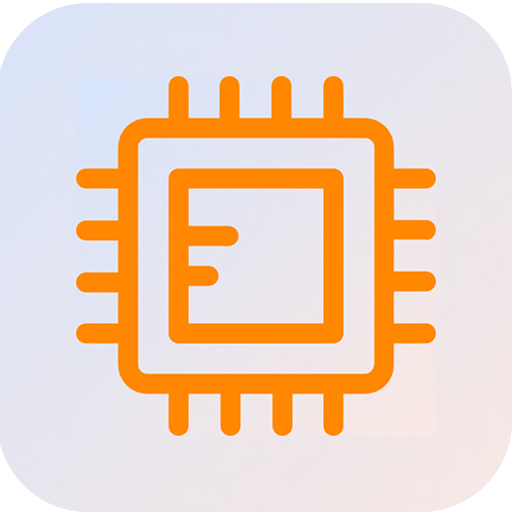
Sensor Control
- Vehicle Speed Sensing
- Engine Speed Sensing
- Brakes
- Torque
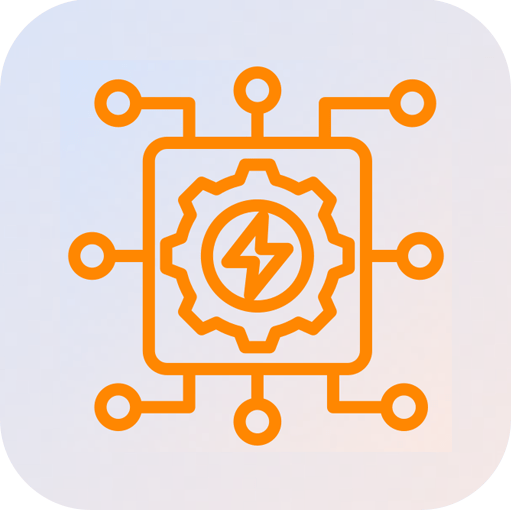
Communication Gateway
- CAN to CAN
- CAN to LIN
- Ethernet to CAN or LIN
- CAN to FlexRay
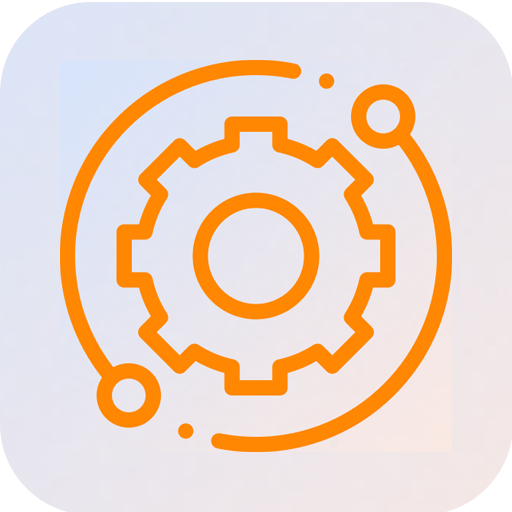
Actuators
- Windshield washer system
- Central locking system
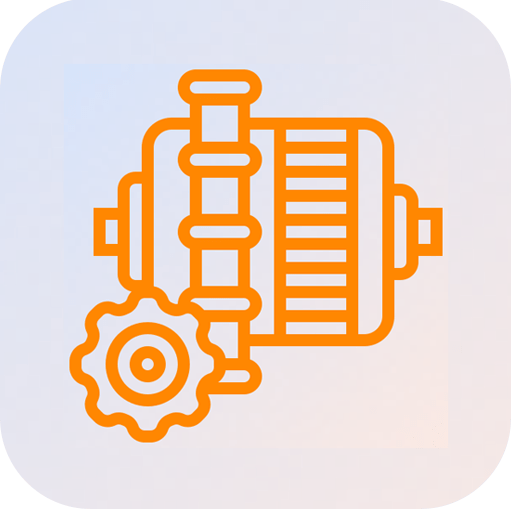
Motor Control
- Seat Adjustment
- Mirror Control
- Power Window
- Sunroof system
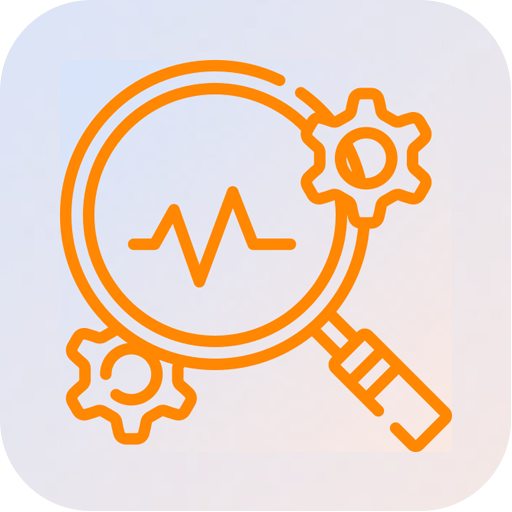
Diagnostics Protocol
- UDS (ISO 14229)
- SAE J1939
- OBD
- DoIP (ISO 13400)
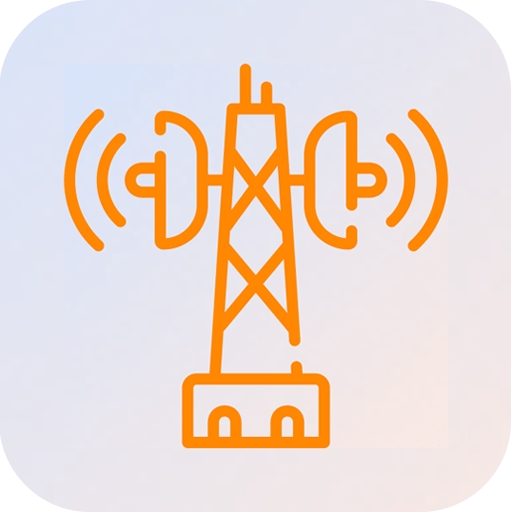
Radio Frequency Communication
- Bluetooth
- GSM / GPS
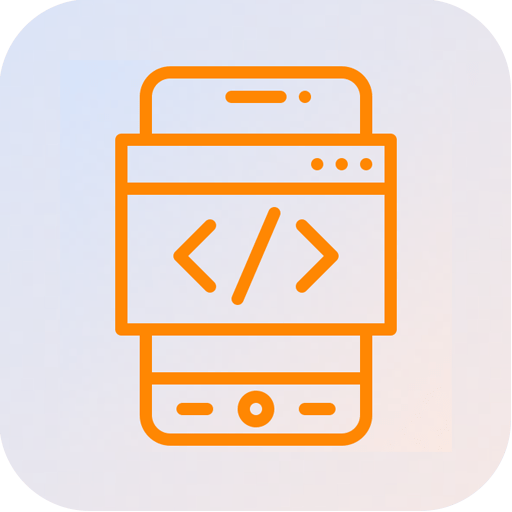
Application Development
- Fuel Level Monitoring
- Gear Advisory system
- Fuel Economy
Technology Architecture of our Body Control Module Platform
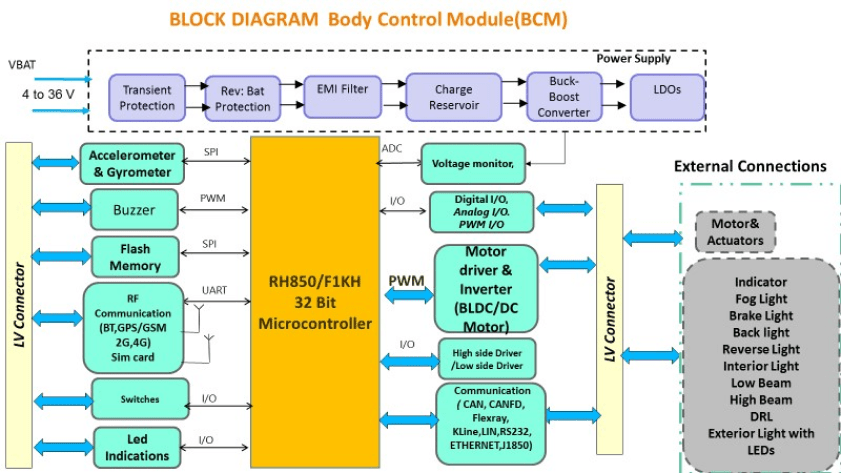
- Our BCM platform is developed on RH850 microcontroller from Renesas.
- Applications are developed using MATLAB/ SIMULINK tools based on MBD methodology.
- Integration of various ECU communication and vehicle diagnostic protocols ensure reduced time-to-market.
- Thanks to its Gateway feature, our BCM solution can co-exist with legacy BCM in the vehicle.
- The BCM platform has been developed as per ISO 26262 standard.
Automotive Electronics Solution Development: HVAC Control System, Seating Control, Power Windows & more
Let’s transform your body electronics product ideas into business reality.
Partner with us for Model Based Development (MBD) of Automotive Electronics (Body Electronics) solutions. Schedule a demo today, to find out how we can reduce time-to-market by leveraging:
- Ready-to-deploy in-vehicle networking and vehicles diagnostics solutions (please add some names with ISO standards)
- And Embedded Software and Hardware design and development expertise.
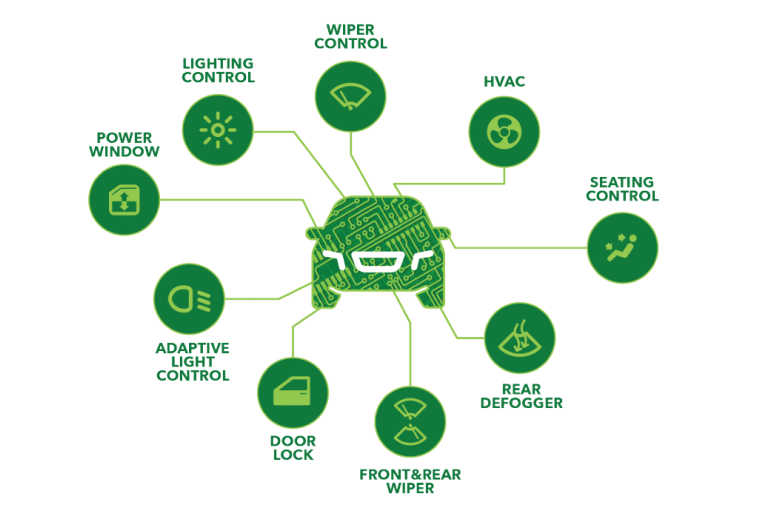
Product Engineering Services: AUTOSAR, MBD, Functional Safety & BCM ECU Testing
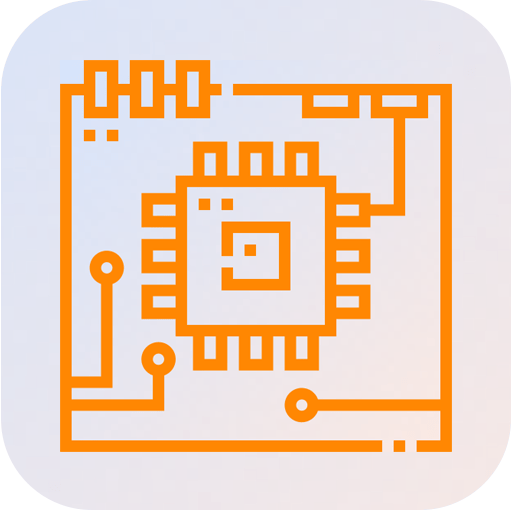
Hardware & Firmware Development
- Automotive-grade hardware and software development services in accordance to the functional safety and reliability norms of ISO 26262
- End to end support in the design and development of Board Support Package(BSP), communication stack for control units (ECU), device drivers, middleware and application.
- Fast and efficient integration of sensors, actuators and motors (BLDC and PMSM motors) for automotive Electronic Control Units (ECU), as per your requirements.
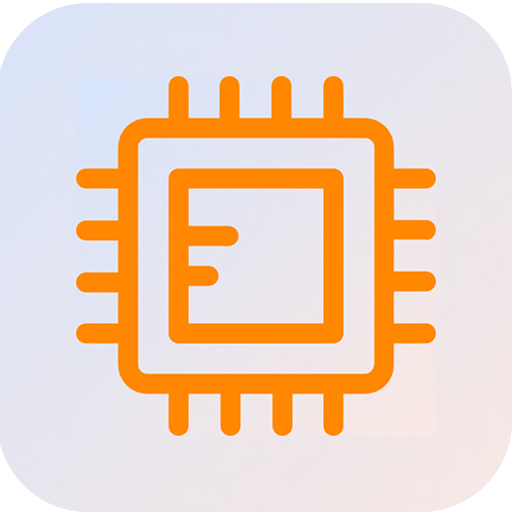
Model Based Development
Ensuring secured communication between the cloud and the IoT gateway through
- Strong player in MATLAB/Simulink and auto code generation (Target Link and RTW)
- Scalable and reliable body control module ECU software and hardware testing services– Model in loop (MIL) testing and Hardware in Loop (HIL) testing
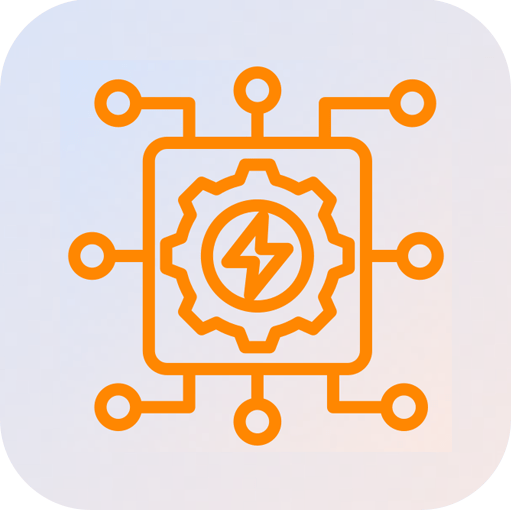
ECU Testing Services
- Embitel offers fully integrated verification and validation services that includes unit testing (white box), integration testing, functional testing, MIL and HIL testing of safety critical body control modules.
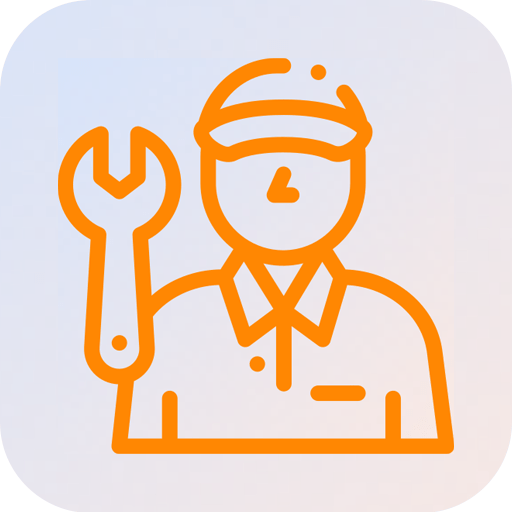
In-vehicle Networking and Vehicle Diagnostics Services
- Pre-tested, pre-packaged as well as ‘re-usable’ automotive stacks to help you with reduced time-to-market and an optimized cost for automotive ECU software development
- Strong domain expertise in in-vehicle network architecture like CAN, LIN, FlexRay, MOST
- Robust integration, configuration and customization solutions for automotive communication and diagnostic protocol stacks – UDS (ISO 14229), SAE J1939, KWP2000, ISOBUS (ISO 11783), OBD2 (ISO 15031)
- Experience in integration of 3rd party automotive stacks as per the best industry standards
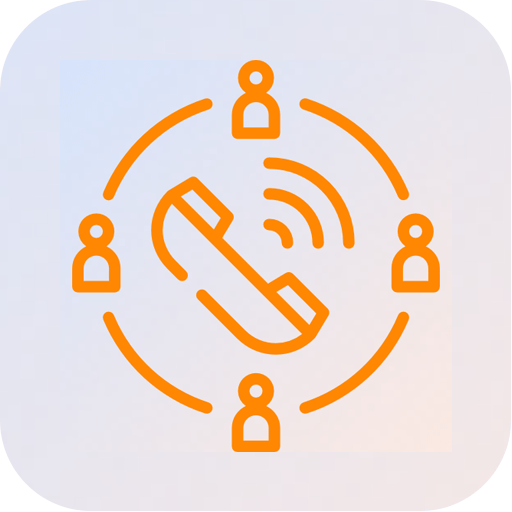
AUTOSAR and ISO 26262 services
- AUTOSAR RTE, BSW and COM stack configuration and integration services as per the industry standards
- Specialised AUTOSAR MCAL development solutions for ECU including– Microcontroller, Communication & I/O Drivers development code generation for tools and automated MIL & SIL testing
- Embitel has a rich experience in a range of AUTOSAR Tools– Comasso, Vector , ECU Spectrum, KSAR AUTOSAR for configuration, DaVinci Developer tool for software architecture design,Pearl and Python for code generation
- Functional safety consulting and development services in compliance with the ISO26262 standards
- Expert solutions for ASIL B, ASIL C and ASIL D complaint automotive electronics (ECU software and hardware)
Related Blogs and Videos: Body Control Modules and Automotive Electronics
Customer Success Stories: BLE, CAN FD stack integration, Model Based Development and more
Learn more about our Automotive ECU success stories including Seating Control Unit Development, Flash Bootloader Software Development, and Model Based Development of automotive ECUs.
We have partnered with global OEMs’ and Suppliers in building efficient body control modules and Electronic Control Unit solutions:
- Model Based Development (MBD) of Automotive Body Control Units
- Model based development of AUTOSAR compliant ECU (Electronic Control Unit)
- Bluetooth Low Energy (BLE) Stack Integration with Seating Control Unit (ECU)
- CAN FD Software Stack Integration for a leading Tier-I supplier
- Bootloader Software Development Project for Seating Control Application
FAQs Regarding Our Body Control Module Reference Design, Architecture and Services
Ans. Our Reference design of the Body Control Module (BCM) supports following features/functionalities:
- Mirror Control
- Window control
- Seat Control
- Lamp Load
- Washer
- Wiper
- Solenoid Control
- Actuator Control
Apart from these, data communication between Instrument cluster control and BCM via CAN is also integrated using re-usable components of our BCM reference design. Our automotive BCM reference design is also equipped with the feature to read data from the sensors. The information may include pressure, fuel level, vehicle/engine speed and others.
Ans. Our body control module supports the most widely deployed vehicle diagnostics protocol in the new age automobiles; viz; SAE J1939, OBD2 (ISO 15031) and UDS (ISO 14229)
J1939 can be integrated for commercial vehicle applications while UDS/OBD can be integrated with passenger vehicles.
Ans. We only provide the reference design for the Body Control Module only. The solution can be customized based on the requirements.
Ans. Following are some of the application level features or the algorithms which are the part of of our body control module reference design:
- Trip Fuel Economy
- Fuel Consumption
- Odometer
- Fuel Meter
- Gear Shift Assistance
- Vehicle speed
- Engine Speed
Ans. There are 3 CAN ports supported by the BCM.
- PCAN- For Power Train
- DCAN- For Diagnostics
- One more CAN sub-network for Cluster and Telematics
Ans. Yes, our BCM reference design is compatible with commercial as well as passenger vehicle.
Ans. Yes, the BCM supports LIN Subnet. If there are certain specific requirements that need LIN to control exterior components like wiper, the same can be integrated in the body control module.
Ans. Our Body Control Module design supports a 5-layered architecture. A model based development approach has been followed to develop this. The base software (BSW) is integrated with application software (can be AUTOSAR compliant , non-AUTOSAR compliant or Model Based Development) depending on the customers’ requirements.
Ans. The BCM reference design has been developed on a MPC5674F Microcontroller from Freescale platform. However, we have expertise in working on a range of microcontroller like Renesas, Fujitsu, Texas, Atmel, Cypress and others.
Ans. Our production ready hardware and software design is built on Android OS using i.MX6 platform.The software features include maps and navigation, touch-less controls (gesture and voice recognition), 3 WiFi cameras, virtual gauges, media streaming, calls and message can be sent and received hands-free.
The hardware used consist of i.MX6 platform, pico-projector, gesture module(IR camera and sensors), WiFi module(IP cameras), sim card slot for GPS and GSM.
Ans. Yes, the body control module reference design has been developed strictly under functional safety guidelines.
Ans. We are supporting XCP and CCP based calibration. These stacks are readily available and can be configured based on the customers’ requirements. In addition, UDS based diagnostic calibration is also supported.
Ans. Our codes strictly adhere to the MISRA C 2012 guidelines.
Ans. We offer the following documentation and testing services for our BCM software:
- Low Level and High Level Design Documentation
- API Documentation for software components
- Module Level Test Plan and Report: Unit testing, functional testing, and integration testing are performed during the product development lifecycle. These tests are carried out on the basis of test case plan and a report is generated post the tests.
- Functional Test Plan & User Acceptance Testing: For the application software, we perform the functional testing and user acceptance testing, for a bug-free code.
- Manual testing: Manual testing is performed for the low level drivers.
- Static Analysis and Script Testing: The static analysis is performed using the Check C tool. Script testing helps in ensuring a Modified condition/Decision coverage.
- Integration Testing: If the BCM application has some additional software component specified by the customer, an integration testing of the software modules is performed.
- Branch Coverage: Branch coverage ensures that each branch of the code is tested for true as well as false cases. This is to prevent any abnormal behavior of the application at any stage.
Ans. Body Control Module is one among the gamut of automotive electronic units in new age vehicles. A BCM is essentially an electronic control system that is controlled by a microprocessor.
Functions such as central door locking, power window, lights, wiper control, seat adjustment, climate control and more are managed by the Automotive BCM solution.
Additionally, it may also act as a gateway for in-vehicle network interfaces and Bus systems to facilitate interactions with other vehicle control units.
Ans. A typical embedded automotive solution of a Body Control Module has the system architecture similar to any other vehicle ECU solution. The components of the same, are as follows:
- A Microcontroller, best suited for the use-case/automotive application
- Communication Interfaces (CAN, LIN, MOST etc.)
- Load Drivers
- Diagnostics Services (UDS, J1939, OBDII)
Ans. An Automotive BCM system works on the basis of input received from the input devices (potentiometers, sensors, magnetic pickup etc.) and the output generated by devices like relay and solenoids. Between these two, are the algorithms and APIs. that define what the action would be and how will it be performed. An example will make things more clear. Let’s consider the example of remote unlocking of the door.
- When a user presses the key on a door lock remote, the RFID (Radio Frequency Identification) module of the BCM receives a signal. It will then verify the frequency of the received signal with the frequency stored in the ECU memory.
- If the frequencies match, it will send the signal to the central locking relay which will perform the required mechanical action to unlock the door.