“Software is not only enhancing a vehicle’s capability but completely transforming it. By-wire technology is a prime example of how deployment of electronics to replace manual systems is changing the face of mobility.”
Car makers have already begun to transform themselves into software firms to embrace the future of mobility. Volkswagen, for example, has invested hugely on its own operating system, automotive cloud, and electronic architecture for all its vehicle brands. Another major automotive player, Toyota is also planning to launch its own operating system by 2025.
When it comes to automotive software, there are various dimensions. There is the body control module that manages seats, automotive lighting, power windows, HVAC and so on. Infotainment system and ADAS are other dimensions in this expansive world of automotive software. While innovations are happening on almost every front, one technology that is taking the industry by storm by its sheer span of deployment is by-wire technology.
By-wire also known as drive-by-wire or x-by-wire refers to electronic system that either replaces or augments mechanical control. Although, the major automotive systems that are replaced by ‘by-wire technology’ are steering, brake and throttle, we will look at other relevant system as well. But first, let’s explore the most common deployments of by-wire systems.
Understanding the Various By-Wire Systems
By-wire technology was first introduced in fighter jets as it became increasingly tough to manoeuvre them using mechanical steering wheels. It took nearly two decades for the automobile industry to introduce the technology in vehicles. Since this started with steering, let’s first understand steer-by-wire technology.
- Steer-by-wire: One of the implementations of by-wire technology is deployed in steering control. The mechanical steering wheel, which is usually attached to the vehicle axle, is replaced by a steering system that has no physical connection to the wheels. This is an important component of a fully autonomous vehicle.
- Electronic throttle control: Unlike traditional throttle control where the gas pedal manually controls the throttle, a true drive-by-wire throttle control uses sensors and actuators to ascertain the position of the gas pedal and open the throttle accordingly.
- Brake-by-wire: Brake-by-wire technology is still at the nascent stage as it requires various fail-safe mechanisms to be implemented. However, anti-lock braking system can be seen as a precursor to brake-by-wire. In principle, brake-by-wire system replaces hydraulic brakes with actuators that activate the brakes in each wheel. Sensors are used to determine the amount of brake force applied by the driver.
Our Experience with Augmenting and Replacing Manual Control with Electronics
By-wire technology essentially is replacing or augmenting manual control with software-driven controls. It is a pre-cursor to the fully autonomous vehicle system where most of the controls including driving is automated.
The automotive team at Embitel has been involved in such technological innovations since the last decade. The learnings and experience from various automotive software development projects have enhanced our capabilities and cemented our position as a leading product engineering company.
To get you up, close and personal with such projects, we got some of the project managers and engineers to share main highlights of their projects. We have compiled a few case studies to help you understand the challenges they were able to mitigate while replacing manual systems with software-based systems.
Case Study-1: Electronic Parking Brake System
An electronic parking brake or electronic hand brake replaces a manually operated hand brake. In this project, the customer required an ASIL D compliant electronic parking brake ECU. A dedicated ECU is responsible for controlling the electronic parking brake. The ECU can be implemented in two different ways. Depending on how the OEM plans to deploy an EPB in the vehicle, we have designed two variants.
Stand Alone: As a stand-alone component, the electronic parking brake ECU activates the parking brake directly using the two actuators.
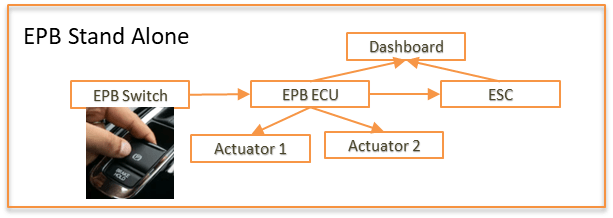
Integrated: In the integrated format, the electronic parking brake ECU is integrated to the electronic stability control system. It activates the parking brake through commands from Electronic Stability Control system.
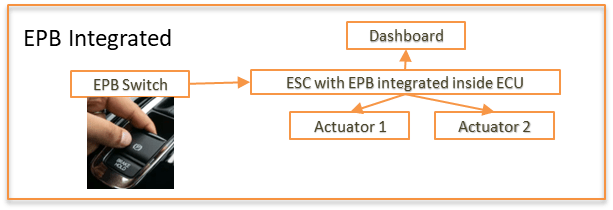
Case Study 2: Seating Comfort and Control System
Seating system in cars have witnessed some striking changes. Whether it is multi-way electronically adjustable seats or customized massage components, vehicle seats have come a long way. Traditionally, the seats could be moved to either front or back using levers. While working for one of our customers, a Tier-1 supplier of automotive components, we were tasked with the responsibility to develop the entire electronic seat control and comfort system that would replace manual seat control. Let’s catch a quick overview of the system.
- A closed loop motor control system powered with HALL sensor controls a motor (actuator) to move the seats front/back and adjust their height.
- Seat recliners are also adjusted electronically by pressing a button or by using an HMI.
The most interesting part of this project is managing any obstacle while seat adjustment is in motion. A special algorithm has been developed to manage such scenarios. Called the Pinch out detection, the algorithm senses any kind of hindrance to the movement and aborts the seat movement. Seat adjustment will be resumed only after the users give fresh commands. Pinch out detection is achieved by HALL output that measures the load on the motor. An obstacle would mean an increased load, which would trigger a PWM signal to abort the operation.
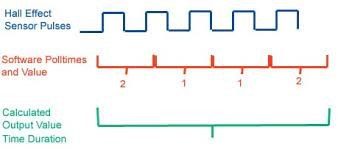
In addition to electronic seat adjustment, various seat comfort systems like massage and lumbar adjustment using pneumatic controls were also part of this project.
Case Study 3: Steering Column Adjustment Control System
Steering column adjustment is a feature that lets the driver adjust the position of the steering wheel. Essentially, there are two movements found in most steering columns- tilt and telescopic. By using tilt adjustment, the height of the steering wheel can be set to the driver’s liking. Telescopic adjustment lets the steering column move back and forth. There is usually a mechanical lever that needs to be unlocked to adjust the steering.
The development of electronic steering column adjustment control system aimed to replace the lever with an electronic system. An electronic control unit is equipped with algorithms to control BLDC or AC induction motors that bring about the required movement of the steering column. Usually, two motors, one to adjust height and the other to adjust the inclination are used.
As a part of this project, the automotive team had to design, develop, and test the motor control application that would be used to adjust the steering column. Apart from the software, Embitel’s hardware team worked on the hardware and architecture design.
Conclusion
By-wire technology has been on a path of innovation. Its implementation has also been diverse. As the automotive industry gets more and more software-driven, we are likely to see several manual systems go electronic.
Embitel’s automotive engineering teams have expertise in transforming manual automotive systems to electronic or by-wire. Our expertise arises from countless such projects combined with a culture of functional safety and cybersecurity implementation. Connect with us to discover how by-wire technology can help you transform your automotive product line.