An automotive system consists of multiple software components that interact with each other.
For instance, a body control module interacts with vehicle seats, door module, sunroof and more.
In the context of ISO 26262 compliant automotive software development, the scenarios get more complicated and nuanced. A fault in a lower ASIL component must not affect the functioning of a higher ASIL component as it can create hazardous situations.
We can take an example of ADAS to understand the extent of this interference. An ASIL B communication module might feed some data to a cruise control module so that the module can take the right decisions in terms of braking and speed control. An instance where the communication module develops some glitch and is not able to feed the right data, can be catastrophic. So how do we avoid such situations? Do we assign higher ASIL to every vehicle component? That would escalate the cost by a significant amount, which is definitely not recommended.
Safety analyses form a huge chunk of safety activities defined in ISO 26262 standard. Different safety analyses have specific outputs to achieve. For instance, FMEA identifies failure modes and their effects. Similarly, FTA analyses the causes or combination of causes that lead to an undesirable event. The bottom line is to detect and eliminate weaknesses in the design and ensure there is no safety goal violations.
Dependent failure analysis (DFA) is one such safety analysis which is very crucial to developing safety-critical automotive systems. To understand its importance in safety-lifecycle and ISO 26262 compliance, let’s get inside the hood of a car.
This is where Dependent Failure Analysis (DFA) can prove to be very effective.
In the subsequent sections, we will try to co-relate dependent failure analysis and Freedom From Interference (FFI). We will examine what goes into dependent failure analysis and how it helps in achieving freedom from interference.
But first, let us understand the dependencies among the components and the types of faults to watch out for.
Why is Dependent Failure Analysis So Important?
Any automotive system or a SOC under design comprises several sub-systems. Many of these sub-systems or sub-blocks may be safety-critical or non-safety-critical. If each of these sub-systems are developed in accordance with their applicable ASIL, the probability of having cascading failures or common cause failures can be ruled out.
This is precisely the reason why DFA is performed along with determination of ASIL. When dependent failures are examined, there are two kinds of failures to be identified- Cascading failures and common cause failures (we have explained in the previous section).
When cascading failures are analysed and found out, the measures to eliminate can be implemented. Freedom from Interference (FFI) is achieved only when cascading failures are eliminated. Usually, FFI is achieved by block partitioning so that a fault detected in one block does not cascade into other blocks.
FFI is just one aspect of dependent failure analysis. In order to achieve independence or technical independence, the functional safety experts must also find out the probable causes of common cause failures. Only by find the causes for both these failures, can the safety measures be implemented.
Understanding Independence, Interference and Freedom from Interference
We mentioned earlier that a fault occurring in one component might have a bearing on another component/s as well. Failure due to these faults are called dependent failures.
When we dig deeper into these failures, we are able to establish their cause and effects.
- When a failure of two or more elements is due to a single specific event or root cause, it is called common cause failure.
- Another kind of dependent failure is cascading failure. In this scenario, failure of one element leads to failure of another. It appears like a cascade of failures, hence the name.
Automotive Functional Safety consultants use the term independence only when the dependent failures (cascading and common cause failures) do not lead to any safety goal violation.
Independence can be ascertained by performing a dependent failure analysis (DFA), which we will discuss later in the blog.
Another term that we must understand before we explain dependent failure analysis is interference. We can understand interference as partially opposite of independence. It is the presence of cascading failure from a non-ASIL or a lower ASIL component to a higher ASIL component that leads to one or many safety goal violations.
Finally, freedom from interference implies absence of cascading failure between elements that leads to safety goal violation. Remember that it does not include common cause failure.
Dependent Failure Analysis, Freedom from Interference and Independence: How Are These Related?
Now that the terms related to dependent failures are clear, we can move to the analysis that help achieve freedom from interference and also independence (hope you are able to identify the difference between the two 😊).
Dependent Failure Analysis focused on finding the single causes/events that invalidates independence and freedom from interference. Every element that might cause such failures are taken into consideration while performing this analysis. Part 6, Part 7, and Part 9 of the ISO 26262 standard document serve as the reference for performing dependent failure analysis.
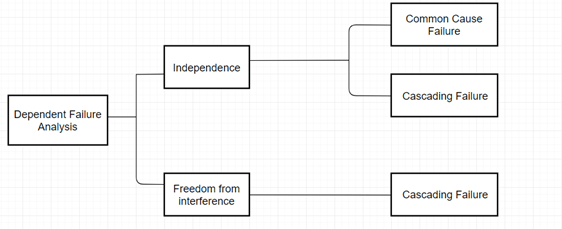
Some points to remember about dependent failure analysis:
- It validates Freedom from Interference between the elements by identifying the cascading failures
- It validates independence between the elements by identifying both cascading and common cause failures
- Dependent Failure Analysis helps in putting in place appropriate safety mechanisms to contain the faults within the element and prevent it from cascading
- Dependent Failure Analysis can be performed at system, software, and hardware level
- The analysis brings forth the points that are susceptible to failures
- It can be performed with both deductive and inductive approaches
What Goes into Dependent Failure Analysis? Stepwise Explainer
Identification of the cause of the failure for all safety-critical elements are recorded in a worksheet. ISO 26262 consultants use tools or regular excel sheets to create the template. Some of the tools that are widely used for dependent failure analysis are Vector PREE Vision, ANSYS medini analyze, ENCO SOX and LDRA tool.
Irrespective of whether you are using tools for analysis or an MS excel sheet, the worksheet has two tabs, one for Cascading Failures (CF) and one for Common Cause Failures (CCF).
Here’s how a typical dependent failure analysis worksheet looks like:
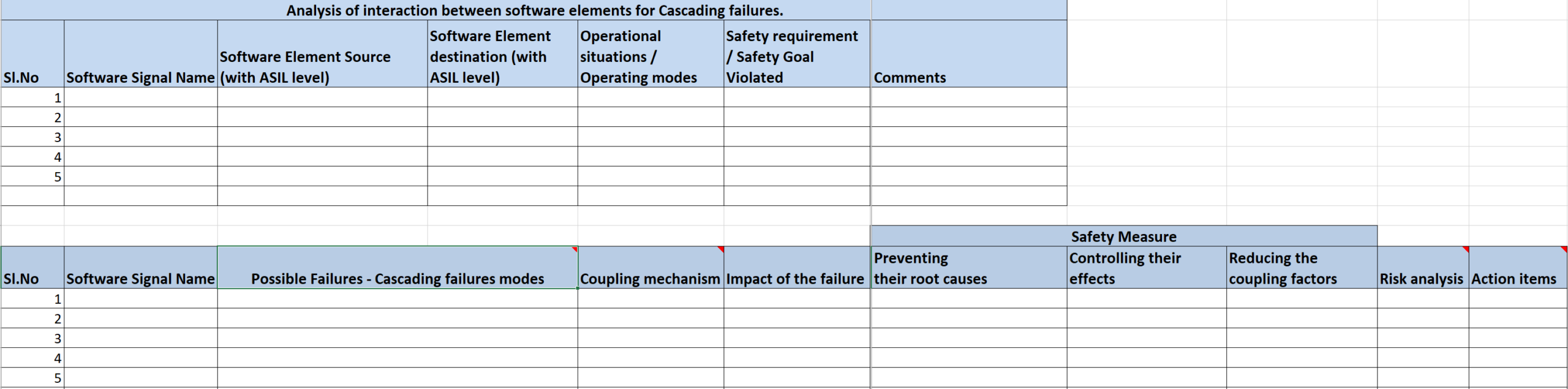

Let’s delve a bit deeper into both CCF and CF analysis.
Common cause failure analysis begins with identifying the elements for which common cause of failure have to be identified. The reason for choosing a couple of these elements must be explained by the engineers. Typically, these activities are performed by automotive experts who are able to identify the elements based on the architecture and their extensive experience in automotive domain.
Some factors that influence the selection of the elements are:
- One software implementing different functions
- Partitioning of software
- Redundant elements
- Same external resource controlling two elements
Following are the aspects based on which the analysis is performed:
- Root Cause of the Failure: The root cause of failure is the common cause (single specific event) that affects both the elements chosen for analysis. For instance, signal processing fault might affect two elements of an LED ECU.
- Failure Mode: These are project-specific failure modes of the elements. Failure modes can be anything from loss of function to degraded functions and unintended activation or deactivation of the element’s function.
- Impact of the Failure: The impact of each failure is documented in this section. Impact at both local and system levels is analyzed. In the context of an LED control ECU, inconsistent switching on and off of an LED can mislead the operator or the driver.
- Safety Measure: The existing safety measures for handling such failures are described in this section. Details about prevention of the root cause and controlling their effects are also an integral part of the analysis and is mentioned here. For instance, if adherence to some automotive standards like CISPR, ISO 11452 etc. can prevent the cause, it must be included in this section.
- Risk Analysis: The risk analysis needs to be performed & documented. If the risk is found to be within the acceptable limits as per the project requirements, then no action is needed, i.e., the action item column in the template need not be filled. If the risk is found to be high & the project decides to change the design, then the action items shall be filled with the change request or the planned changes to mitigate\handle the risk.
- Action Item: The design changes resulting from the CCFA constitute the action items. These are changes that are required to be made to the design in order to keep the impact of the failure as localized as possible.
Cascading failure is analyzed between the source element (origin of fault) and destination element which is the final failure perceived by the vehicle driver. These elements are identified during the software architecture design activity. Analysis of data exchange between source and destination elements is performed in order to identify the signals transmitted by source element that caused the cascading failure.
The ASIL assigned to the source and destination element between which the data exchange took place is also analyzed. It is also extremely important to consider the operating modes and situations that are relevant to the cascading failures and hence, must be listed.
Apart from these factors, failure modes, their impact, and ways to control them are analyzed and documented. These analyses go a long way in achieving freedom from interference and identifying the design changes required to reduce the risk of dependencies.
Following possible failures must be looked out for during cascading failure analysis:
Timing and Execution: Timely execution of processes is paramount to automotive software. Failures such as blocking of execution, execution deadlocks, processes going to infinite loop, incorrect time allocation for execution and issues with synchronization among the elements are some of the failures related to time and execution that must be analyzed.
Memory Corruption: If an element is corrupting the memory of another element or accessing the memory that is allocated to a different element, it can lead to cascading failures. Such interactions must be identified and documented.
Information Exchange: The information exchange between the elements must be accurate and there must not be any loss, repetition, corruption, and delay in information exchange. Other factors such as incorrect addressing, information sequence also need to be analyzed.
Top Down (Deductive) vs Bottom-up (Inductive) Approach to Dependent Failure Analysis
Top down and Bottom-up are two approaches to analyse any given failure. Top-down approach follows a deductive analysis paradigm where the FuSa analyst begins from the top-level failure or a safety goal violation.
Such failures and violations are first broken down to understand the failure modes and further dissected to identify the dependent failures i.e. cascading, common cause or independent failure. Next step is to identify the potential risk that can emanate from the dependent failure. Deductive analysis is recommended at the architectural design phase as it gives important inputs for taking design decisions.
Bottom-up or the inductive approach comes at a later stage when architecture design is at a more refined level. Here, we start with a set of initiating causes and analyse the failures they may cause.
FMEA also provides some input for an effective and comprehensive DFA. Similar parts or components with similar failure modes that appear several times in an FMEA can give additional information about the potential for dependent failures.
Top down combined with bottom-up approach of performing DFA gives a complete picture of the dependent failures and contribute to meeting functional safety requirements.
Conclusion
ISO 26262 standard makes different analyses a very important part of safety lifecycle. Dependent failure analysis is one such analysis that helps achieve freedom from interference and independence. It demonstrates that requirements to reduce the dependencies between the elements have been met and are in sync with the technical safety requirements and functional safety requirements. At the end of the analysis, the engineers have clear insights on the common and cascading failures which help them reinforce the safety measures.