Prior to the invention of the electric starter motor, a hand-crank was used to manually turn the engine on. This was a difficult and dangerous task, as the crank could kick back and injure the person cranking the engine.
In 1911, a man named Charles Kettering developed the first electric starter motor. The starter motor used an electric motor to turn the engine, and was operated using a key or button. This innovation revolutionized the automobile industry.
More than a century on, electric motors have come of age in the automotive industry, and BLDC (brushless DC) motors are leading the charge.
The adoption of BLDC motors in the automotive industry has been increasing steadily over the past few years. As more controls transition from manual to automated, the demand for BLDC motors is on a rise.
A Sneak-Peek into the History of Automotive DC Motors
Traditionally, all automotive components like power windows, wiper systems, power steering, seating control, traction control system, etc. relied heavily on Brushed DC Motors.
Reason- Brushed DC Motors had the ability to reach peak speed in a matter of seconds.
However, wear and tear in Brushed DC Motors was a major drawback. Also, controlling the speed in such a motor was not easy. These, along with several other reasons, led to the widespread adoption of Brushless DC (BLDC) Motors in the automotive industry.
Sounds like an interesting piece of technology-related history, right? We will delve deeper into this topic, but before that, let’s brush up our basics a bit.
Brushed Vs Brushless DC Motors
Brushed and Brushless DC Motors have 2Â basic components-Â Stator and Rotor (also called armature).
In a Brushed DC Motor, brushes are present as additional components.
While both Brushed DC Motors and BLDC Motors are driven by permanent magnets or electro-magnets as the stator, the difference lies in the commutation.
How Does a Brushed DC Motor Work?
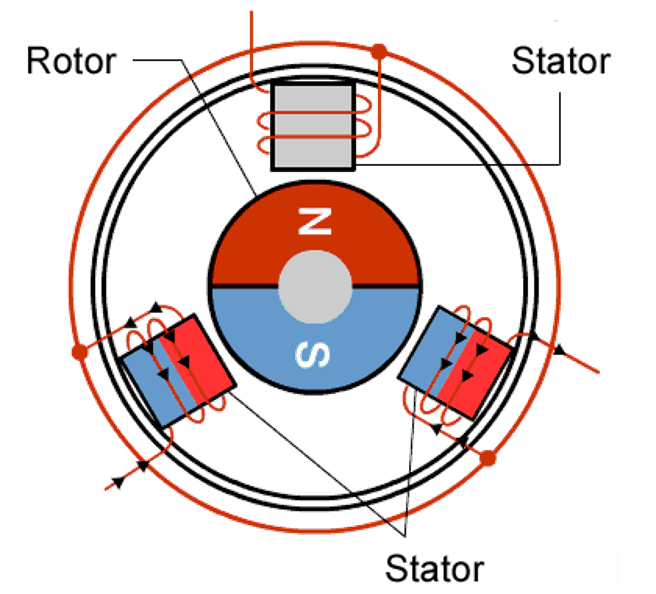
- Rotor, a permanent magnet, generates a stationary magnetic field around the stator.
- When DC power is applied to a phase of the stator coils, the coils become energised and function as an electromagnet.
- The force interaction between this permanent magnet and the electromagnet is what drives the BLDC Motor.
Motor Rotation – Energising of the Stator Coils and Movement of the Rotor
|
As brushes and commutator come in contact with each other and the rotor winding, it gets worn out very frequently.
Automotive Applications Best Suited for BLDC Motors
BLDC (brushless DC) motors have numerous applications in an automobile, some of which are as follows:
- Electric Power Steering (EPS): BLDC motors are used in EPS systems to provide the necessary power assistance for steering. The motor is responsible for turning the steering wheel, and the amount of assistance provided is controlled by an electronic control unit (ECU).
- Electric Braking System: BLDC motors are used in electric braking systems to provide the necessary braking force. The motor is responsible for applying pressure to the brake pads, and the amount of force applied is controlled by an ECU.
- Electric Powertrain: BLDC motors are used in electric powertrains for hybrid and electric vehicles. The motor provides the necessary torque to propel the vehicle, and the speed is controlled by an ECU.
- Cooling Fan: BLDC motors are used in cooling fans to provide the necessary airflow to cool down the engine and other components. The motor speed is controlled by an ECU based on the temperature of the engine.
- HVAC Blower: BLDC motors are used in HVAC (heating, ventilation, and air conditioning) systems to provide the necessary airflow for cabin comfort. The motor speed is controlled by an ECU based on the temperature and humidity inside the cabin.
- Wipers: BLDC motors are used in wiper systems to provide the necessary motion for the wiper blades. The motor speed is controlled by an ECU based on the intensity of rain detected by sensors.
Now, let us understand how Brushless DC Motors help in overcoming this issue of wear and tear.
How Do Brushless DC Motors Work Without Wear and Tear?
Since there are no brushes in a BLDC Motor, it relies on an electronic system (external motor control system) for commutation.
For ease of understanding, let’s discuss the working of the most commonly deployed 3 phase Brushless DC Motor:
- In this motor, the switching of current in the motor phases (commutation) is done in a 6-step pattern.
- These commutation phases move the electromagnetic field. This, in turn, moves the rotor and the motor shaft.
- The motor control system generates PWM signals that assist in energising the motor phases at the right time.
- BLDC Motor systems can also be fitted with Hall Effect sensors, in order to improve the overall efficiency of the motor.
- A Hall Effect sensor helps define the accurate position of the stator with respect to the rotor. This is essential for the optimum functioning of the motor.
A Snapshot of Brushed Vs Brushless DC Motors
Parameter | Brushed DC Motor | Brushless DC Motor |
Commutation | Commutation is achieved by brushes and copper commutators | Commutation is achieved electronically using motor control system |
Wear and tear | Presence of brushes causes wear and tear | Wear & tear is minimum as brushes are absent |
High torque | Peak speed can be reached fast but not suitable for high torque application | Capable of producing high torque and constant speed |
Use cases | Used in basic automotive applications like wipers and power windows | Deployed in electronic power steering, HVAC systems |
Efficiency | Moderate | High |
Regular maintenance | Periodic maintenance required | Limited/none |
Dynamic Response | Slow | Low rotor inertia; hence fast |
Electric Noise | High | Low, due to the absence of arcs from brushes that generate noise |
Why Did the Automotive Industry Embark on This Great Migration to BLDC Motors?
The difference in the construction and working of brushed and brushless motors offer enough reasons for the automotive industry to upgrade to BLDC Motors.
Let’s look at some of these advantages in detail:
- An increase in efficiency of about 15-20% is offered by electronically controlled Brushless DC motors.
- There is a marked reduction in maintenance cost, as there are no brushes in BLDC Motors
- Brushless DC motors are more cost-effective, when we take into consideration the need to periodically replace brushes in Brushed DC Motors (due to wear and tear).
- Smaller size, lesser noise, enhanced heat dissipation and higher speed also make BLDC Motor a preferred choice for automotive applications.
- Since BLDC Motors can be integrated with electronics-based advanced motor control systems, these are ideal solutions for modern automotive applications like EPS (Electronic Power Steering), HVAC Systems, Electric Vehicle Drivetrain.
Point to note – BLDC Motors are more expensive as far as initial investment is concerned. This is primarily due to the need for design and development of motor control systems. However, the advantages offered by these motors far outweigh the additional investment.
What Challenges Would Your Team Face During the Migration from Brushed DC to BLDC Motors?
Migration from Brushed DC Motors to its brushless relatives comes with its own set of challenges.
Of all the issues that one may face during the migration process, overcoming the challenge related to commutation is the most critical.
A Brushed DC Motor relies on mechanical commutation with brushes and a copper commutator, and this controls the direction of the motor rotation.
A BLDC Motor, in contrast, has several other capabilities. This includes features like soft start/stop, diagnostics capability, FOC algorithm for better efficiency and various other software-level functionalities.
Most of these features are facilitated by the BLDC motor controller.
While in Brushed DC Motors, the switching of the magnetic field is only limited to two phases, BLDC Motors are mostly 3-phased. Hence, the switching of current is done for three phases.
While migrating to Brushless DC Motors, either of the following commutation sequences can be adopted:
- The classical and simple Trapezoidal Control (6-step commutation)
- The advanced FOC with Space Vector PWM
For accurate commutation in a BLDC Motor, the motor position is very important. Components like Hall Effect sensors, Resolvers and Encoders are deployed in the BLDC motor controller as feed-back mechanisms. This helps in achieving the required accuracy of the motor position.
Sensor-less option for commutation of BLDC Motor is also used in some applications. The back EMF provides the feedback mechanism in such cases. However, FOC algorithm (Vector Current Handling) is a more efficient method of commutating BLDC Motors.
Integrating Vector Current Handling requires a great deal of experience and expertise in Control Systems and motors.
Software Components That Can Be Reused During Migration to a BLDC Motor
Certain software components like communication stacks can be reused in the process of migration from Brushed to Brushless DC Motor. However, there are certain aspects to be considered while doing so.
The underlying hardware platform and other hardware components like current sensors must be similar. If there are changes in the hardware components, some customisations may be required in the following software components:
- Hardware Abstraction Layer
- MCAL Layer
The motor drive logic and application layers mostly remain unchanged while migrating from Brushed DC Motor to BLDC Motors. Vehicle Diagnostics and In-vehicle Network Protocol Stacks can be easily reused without any change.
How is the Migration to BLDC Motors Manifesting Itself in the Automotive Industry?
The migration has been quite fast paced. The modern automotive industry is experimenting with a lot of new technologies and BLDC Motors seem to fit the bill.
In fact, applications like traction control, which were once synonymous with Brushed DC Motors are now being designed using BLDC motor controllers.
In the case of an automotive seating control system, the humble Brushed DC Motor would not be able to efficiently perform all the operations. Hence, the shift to Brushless DC Motors with BLDC motor controllers for accurate operations is inevitable.